Electromagnetic Vibrating Feeder
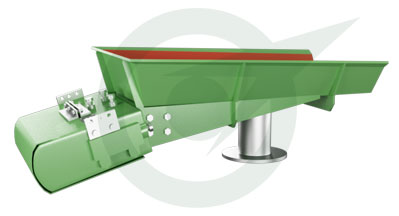
Star Trace vibrating feeder are used in processing industries for handling all types of materials such as hot, damp, lump, dusty or abrasive for various function like flow of material from storage, proportioning and bending, packing, mixing, weighting, sprinkling, scalping, crushing, washing, drying, heating, cooling, dusting, spreading, batching and etc.
Known for their corrosion resistance and high performance, heavy-duty electromechanical feeders are used to increase the bulk handling productivity with controlled high feed rates which further results in improvement of cost-per-ton handling efficiency. These feeders include electromagnetic feeders, electromechanical vibratory feeders, inclined vibro grizzly feeder, vibratory furnace charger. These are ruggedly constructed to minimize the maintenance and improve the production efficiency.
All our feeders need separate controllers and have very dependable, flexible solid-state control. The feed rates are adjustable and the response is prompt. The electromagnetic design offers durable and reliable service. Drives are encased in dust-tight housings. Controls include a simple rheostat type variable speed controller.
- The Electromagnetic Vibratory Feeder consist of a tray made out of Mild steel or Stainless Steel and the body housing.
- The body housing of the Vibrator is made from Heavy duty M.S.Plates.
- As the Magnet get energized the Vibration sets the material in motion.
- The controller of Vibrator gives the controlled flow of the material.
- The housing of the Electromagnet is made in totally enclosed design make it dust proof.
With an appropriate deck slope, high-frequency vibration affords conveying speeds as high. This vibration is maintained even with varying line power fluctuation.
Electrical pulses in the coils create a series of magnetic pulls that attract the armature and the deck. Restoring forces in the bar oppose each pull, causing the armature to spring away from the magnet. At an electrical frequency of 60 cycles per second, the armature and the deck operate at 3,600 times per minute (the vibration rate of the feeder). Material is moved by a series of "jumps" that correspond to the frequency of the vibrations. The distance the bars travel can be changed by varying the voltage to the coils. With this variation in the length of each "jump," or vibration amplitude, the conveying speed of the material on the feeder deck changes, resulting in a capacity rate that fits your requirements.
These can take one of four forms, bonded rubber mounts, hollow rubber mounts, helical coil compression springs or helical coil tension springs. The type of mount is selected to suit the requirements of the installation and to provide a minimum isolation efficiency of 95%.
The range of Hopper Feeders has been designed as a self discharging bulk storage hopper capable of storing and then discharging components or materials in a controllable, continuous stream. Particularly suitable for components or products that tangle or do not feed well from static hoppers, the hopper feeder eliminates many of the interruptions in production that can occur with more conventional systems.
Hopper Feeders are essentially closed two mass oscillation systems, sub-critically tuned. The vibratory drive unit and structure are designed to give an asymmetric displacement of the conveying plane which results in a progressively increasing product velocity towards the discharge end of the hopper. This motion prevents mass flow and creates an untangling and thinning out effect on the material / parts being handled, reducing them to a manageable quantity. Special low frequency, high amplitude units are available for products which are particularly difficult to handle.
- Easy & stepless variation of delivery of material either manually or automatically possible.
- Delivery remains generally constant in spite of fluctuations in supply voltage.
- Drive is extremely robust and simple in construction.
- Electromagnetic drive is dustproof and is impervious to moisture.
- Abrasives Industries
- Ceramics Industries
- Chemical Industries
- Fasteners
- Fertilizers
- Food Industries
- Foundry Industries
- Pharmaceutical Industries
- Plastic Industries
- Paper & Pulp Transportation Industries